CNC Machining Parts Supplier: Elevating Your Manufacturing Needs
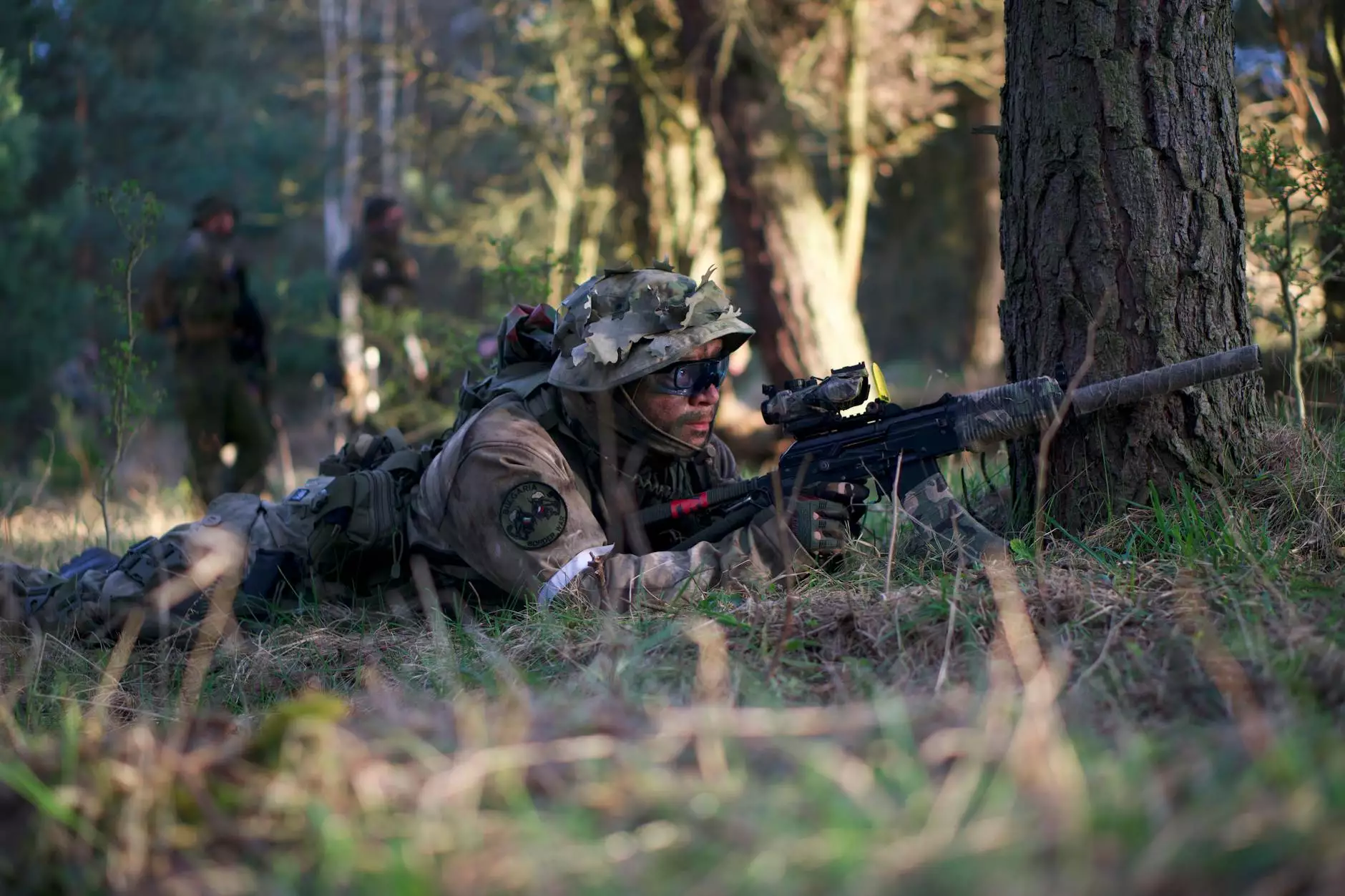
In today's fast-paced industrial landscape, having reliable suppliers is crucial for any manufacturing business. Among the leading solutions providers are CNC machining parts suppliers, which play a pivotal role in ensuring that businesses have access to precisely manufactured components needed for their operations. This article explores the numerous advantages of collaborating with a dedicated CNC machining parts supplier, emphasizing their relevance in the metal fabrication industry.
Understanding CNC Machining
CNC, which stands for Computer Numerical Control, refers to the automation of machine tools through the use of computers executing pre-programmed sequences of machine control commands. This technology revolutionizes how parts are manufactured, providing highly accurate and repeatable results. CNC machining parts suppliers offer a broad range of services, including:
- Precision Machining: Parts are crafted with high accuracy for both small and large batches.
- Material Versatility: Suppliers can work with various materials, such as metals, plastics, and composites.
- Custom Design: Tailored solutions that meet specific requirements of clients.
- Rapid Prototyping: Quick turnaround times for prototype parts to assess designs before mass production.
Why Choose a CNC Machining Parts Supplier?
1. Superior Quality Assurance
Quality is non-negotiable in manufacturing, particularly when precise components are critical for operation. A reputable CNC machining parts supplier employs strict quality control measures to ensure that every part meets industry standards. This includes:
- ISO Certification: Many suppliers are ISO certified, ensuring they adhere to international quality management principles.
- Advanced Inspection Techniques: Suppliers utilize the latest technology for inspection and quality assurance, including coordinate measuring machines (CMM) and laser scanning.
2. Cost Efficiency
While the initial investment in CNC machining might seem high, partnering with a CNC machining parts supplier can lead to significant cost savings in the long run. Here’s how:
- Reduced Waste: CNC machining minimizes material wastage through precision cutting.
- Lower Labor Costs: Automation reduces the need for manual labor, which can lower production costs.
- Economies of Scale: Many suppliers offer tiered pricing based on volume, making larger orders more affordable.
3. Enhanced Speed and Efficiency
Time is a crucial factor in manufacturing and using a CNC machining parts supplier can significantly enhance production speed. Their capabilities allow for:
- Rapid Cycle Times: CNC machines operate quickly and can produce complex parts with speed and efficiency.
- Consistent Production Rates: Automated processes lead to consistent output, minimizing downtime.
- Shorter Lead Times: Suppliers can often deliver parts faster than manual methods, thanks to their advanced technology.
Best Practices for Selecting a CNC Machining Parts Supplier
1. Evaluate Expertise and Experience
When searching for a CNC machining parts supplier, assess their experience in the industry. Consider parameters such as:
- The years in business.
- The range of services provided.
- The industries they serve, ensuring they align with your manufacturing needs.
2. Review Client Testimonials and Case Studies
Genuine feedback from previous clients provides insight into the supplier’s reliability and quality of work. Look for:
- Success Stories: Case studies showcasing how the supplier overcame challenges for clients.
- Client Retention Rates: High retention rates often indicate a supplier that delivers quality and satisfaction.
3. Request Samples and Quotes
Always request samples of their previous work and detailed quotes. This practice helps you gauge the supplier’s capabilities and ensure they can meet your budget:
- Compare Quotes: Ensure you get multiple quotes to compare prices and services.
- Inspect Samples: Analyze the quality and finish of their products.
Future Trends in CNC Machining
The CNC machining landscape is continually evolving. Staying informed about future trends can help businesses remain competitive. Key trends to watch include:
- Increased Automation: The trend toward more automated solutions enhances operational efficiency.
- Integration of AI and IoT: Smart manufacturing with connected machines can lead to optimized processes.
- Advanced Materials: Ongoing research and development will lead to new materials, enhancing the range of applications.
Conclusion
In summary, partnering with a dedicated CNC machining parts supplier like Deep Mould can redefine your manufacturing operations through superior quality, cost efficiency, and speed. The capability to produce tailored solutions that fit specific industry needs makes CNC machining an invaluable resource in today’s competitive market. Evaluate potential suppliers carefully to establish a long-term partnership that propels your business forward.
Investing in CNC machining services is not merely a tactical choice; it is a strategic decision that can lead to innovation and growth within your organization. By choosing the right supplier, such as those found at deepmould.net, you ensure that your manufacturing process remains cutting-edge and competitive for years to come.