The Ultimate Guide to Pressure Die Casting Moulds in Metal Fabrication
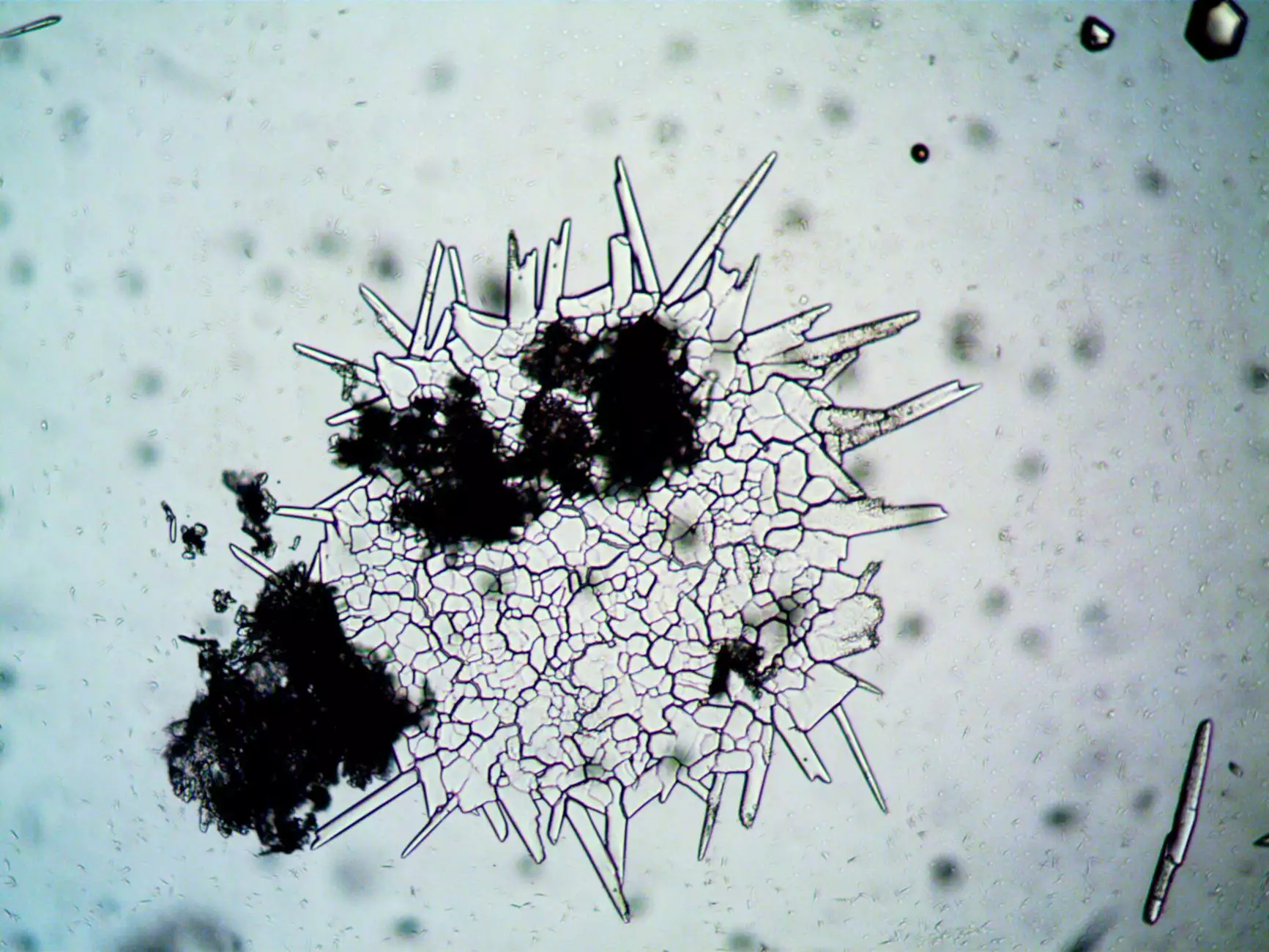
In the world of metal fabrication, the process of die casting holds significant importance, especially when it comes to producing complex parts with high precision. Among the various methods available, pressure die casting emerges as a front-runner, primarily due to its efficiency and cost-effectiveness. This article delves deep into the intricacies of pressure die casting moulds and their pivotal role in the manufacturing processes across various industries.
What is Pressure Die Casting?
Pressure die casting is a sophisticated manufacturing process that involves forcing molten metal into a mould under high pressure. This method allows for the production of detailed and intricate components that can meet the stringent quality requirements of different sectors, including automotive, aerospace, and consumer electronics. The use of pressure die casting moulds in this process is essential for achieving the desired shapes and tolerances.
The Process Explained
The die casting process can be broken down into several key steps:
- Melting the Metal: The chosen metal, often aluminum, zinc, or magnesium, is melted in a furnace at high temperatures.
- Injecting the Metal: Once molten, the metal is injected into a steel mould at high pressure using a plunger mechanism.
- Cooling and Solidification: The metal is allowed to cool and solidify in the mould, forming the desired shape.
- Removing the Casting: After sufficient cooling, the mould is opened, and the casting is removed.
- Finishing: The casting undergoes further machining or finishing processes as required for quality assurance.
Advantages of Using Pressure Die Casting Moulds
Pressure die casting moulds offer numerous advantages that make them a preferred choice in metal fabrication:
- High Precision: The process allows for tight tolerances and excellent surface finishes, reducing the need for additional machining.
- Efficiency: With rapid cycle times, manufacturers can produce large volumes of die cast parts quickly.
- Complex Geometries: Pressure die casting can create intricate shapes that would be challenging or impossible with other methods.
- Material Utilization: The process minimizes waste, making it a more sustainable option within manufacturing.
- Cost-Effectiveness: The initial costs for mould creation can be high, but the long-term savings on material and labor can offset this investment.
Materials Used for Pressure Die Casting Moulds
The materials selected for pressure die casting moulds are crucial in determining the success of the casting process. Common materials include:
- Steel: Often used for its durability and ability to withstand high pressures and temperatures. Variants like H13 tool steel are particularly popular.
- Aluminum Alloys: Used mainly for low-to-medium volume productions due to their lower cost compared to steel.
- Nickel-Based Alloys: Useful for applications that require high resistance to wear and corrosion.
Key Considerations When Choosing a Pressure Die Casting Mould
When selecting a pressure die casting mould, several factors must be considered:
Dimensional Accuracy
Understanding the specific tolerances needed for your parts is crucial. Pressure die casting can achieve very tight tolerances, so ensure your mould design considers these requirements.
Complexity of Design
Consider the part's design complexity; if the design is intricate, the mould must accommodate undercuts and draft angles for easy release of the finished casting.
Cost and Production Volume
The cost of creating a die casting mould can be significant. It’s essential to evaluate the production volume required to justify the initial investment.
Material Compatibility
Choose materials for the casting and mould that are well-suited for one another. This compatibility affects the quality and durability of the parts produced.
The Role of Deep Mould in Pressure Die Casting
At Deep Mould, we specialize in providing high-quality pressure die casting moulds tailored to every customer’s unique specifications. Our team of experts is dedicated to optimizing the manufacturing process, ensuring every mould meets rigorous standards of precision and reliability.
Our Expertise
With years of experience in the metal fabrication industry, Deep Mould employs advanced techniques and technologies to deliver top-notch moulds. Our services include:
- Custom Mold Design: Tailored designs that meet your specific requirements.
- Rapid Prototyping: Quick turnaround on prototypes to speed up the production process.
- Material Selection Guidance: Expert advice on the best materials to use for your projects.
- Post-Production Support: Ongoing assistance after production to ensure quality control.
Future Trends in Pressure Die Casting
As technology evolves, so does the field of pressure die casting. Several trends are shaping its future:
Automation and Robotics
The integration of automation and robotics in the pressure die casting process is enhancing efficiency and precision. Automated systems can manage the casting process, allowing for quicker cycle times and reduced labor costs.
Advanced Materials
Research into new materials continues to evolve, with advances in lightweight materials enabling manufacturers to produce stronger, lighter parts that enhance performance across industries.
Sustainability Initiatives
With a growing emphasis on sustainability, the pressure die casting industry is exploring methods to reduce its environmental impact, such as improved recycling processes and energy-efficient technologies.
Conclusion
In conclusion, the significance of pressure die casting moulds in the manufacturing landscape cannot be overstated. Their ability to produce high-quality, complex components quickly and cost-effectively makes them indispensable in metal fabrication. Whether you are an experienced manufacturer or new to the field, recognizing the advantages and intricacies of pressure die casting moulds will position your business for success.
If you are looking for unparalleled expertise in designing and producing pressure die casting moulds, consider partnering with Deep Mould. Contact us today to discuss how we can meet your manufacturing needs and help you stay ahead in your industry.