Exploring Plastic Injection Mold Shops: The Heart of Manufacturing Innovation
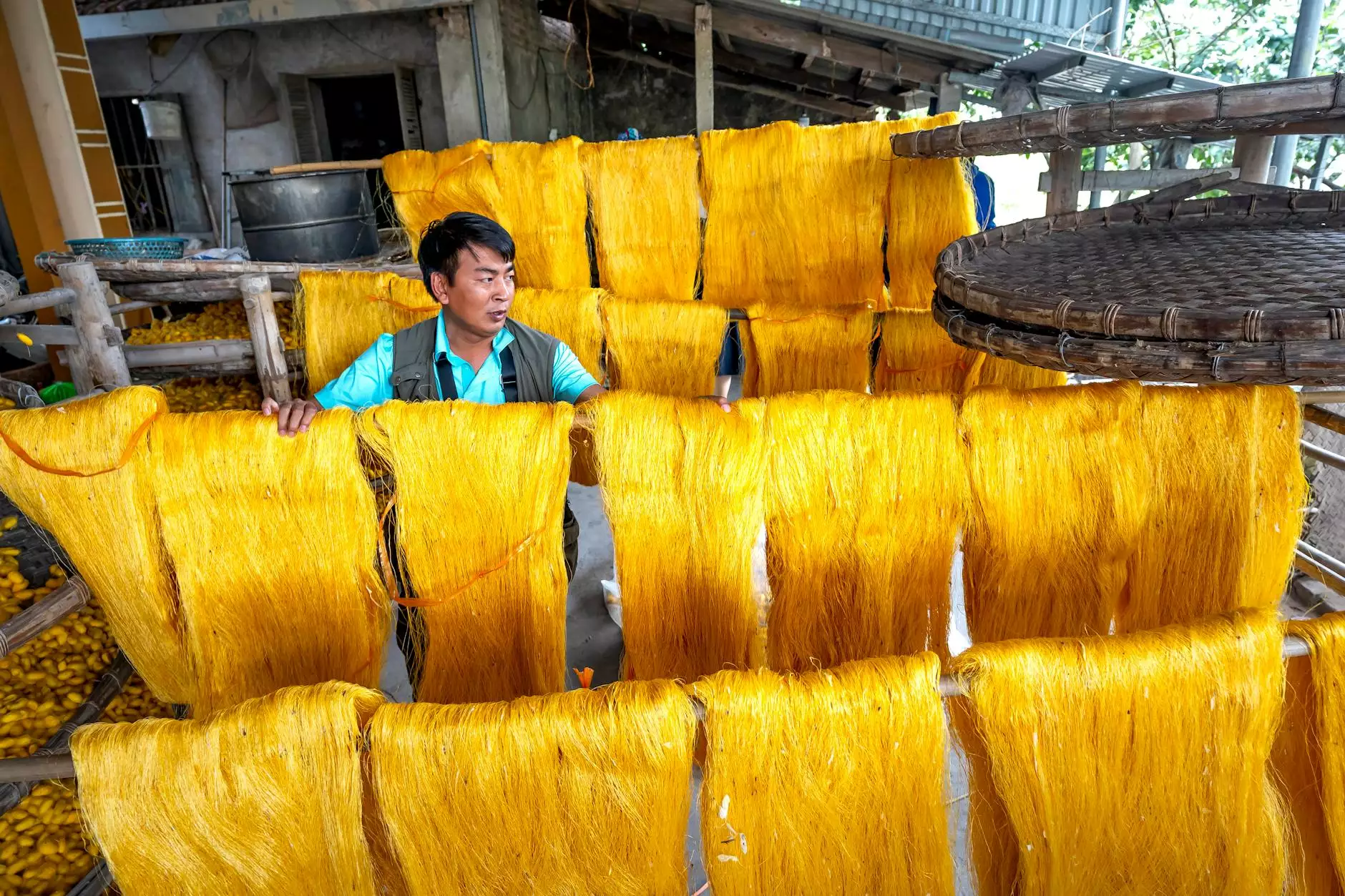
In today's world, where technology propels industries forward, plastic injection mold shops stand out as the backbone of manufacturing. These specialized facilities play a crucial role in creating complex parts and products used across various sectors, ranging from automotive and electronics to consumer goods and medical devices. This article delves deep into the intricacies of plastic injection mold shops, their processes, advantages, and the future of this vital industry.
The Importance of Plastic Injection Mold Shops
Plastic injection mold shops are essential for transforming raw plastic materials into usable products. The importance of these facilities can be summarized in several key aspects:
- Efficiency: They enable mass production of plastic parts at a rapid pace.
- Precision: Modern mold shops employ advanced techniques to ensure high accuracy and quality.
- Cost-effectiveness: With large production runs, the per-unit cost of plastic components decreases significantly.
- Innovation: These shops foster innovation by allowing designers to create complex geometries that were previously impossible to manufacture.
Understanding the Process of Plastic Injection Molding
The process of plastic injection molding involves a series of intricate steps, each critical to the final outcome. Here's a breakdown of the process:
1. Material Selection
The journey begins with selecting the right polymer material for the intended application. Common materials include:
- Polypropylene (PP)
- Polyethylene (PE)
- Polystyrene (PS)
- Acrylonitrile Butadiene Styrene (ABS)
2. Mold Design
Once the material is chosen, skilled engineers design a mold that will shape the liquid plastic into the desired form. This design phase involves:
- 3D modeling
- Simulation of the injection process
- Calculating cooling times and cycle times
3. Injection Process
In this stage, the selected plastic is heated until it becomes molten and is then injected into the mold under high pressure. This ensures that the material fills every cavity, capturing fine details.
4. Cooling
After the injection, the mold is cooled, allowing the plastic to harden into the desired shape. Proper cooling time is essential to prevent warping and maintain structural integrity.
5. Ejection
Once cooled, the mold opens, and the finished part is ejected. This step must be executed delicately to avoid damaging the newly formed plastic piece.
6. Finishing Touches
Finally, additional processes may be applied to enhance the product, such as:
- Trimming excess material
- Surface treatment and finishing
- Assembly if multiple parts are required
Advantages of Using Plastic Injection Mold Shops
Utilizing plastic injection mold shops provides numerous benefits to businesses. Some of the key advantages include:
Scalability and Flexibility
Injection molding allows manufacturers to transition from small runs to large-scale productions with ease. This scalability is particularly beneficial for companies looking to grow their market reach without incurring excessive startup costs.
Consistent Quality
With injection molding, manufacturers can achieve near-identical products across batches due to the precision of the molds. This consistency is crucial in maintaining brand reputation and customer satisfaction.
Reduced Waste
The injection molding process minimizes waste material when compared to other manufacturing techniques. By recycling excess plastic, mold shops promote environmental sustainability while reducing production costs.
Enhanced Safety Features
Modern mold shops utilize processes that improve worker safety, including automated systems and advanced machinery designed to reduce human error and accidents.
The Future of Plastic Injection Mold Shops
As industries evolve, plastic injection mold shops must adapt to stay competitive. Future trends shaping the industry include:
1. Automation and Industry 4.0
The integration of automation and smart technologies (often referred to as Industry 4.0) is transforming plastic injection mold shops. Automation leads to:
- Reduced labor costs
- Improved production speeds
- Enhanced data analytics for operational efficiency
2. Sustainable Practices
With growing environmental concerns, plastic injection mold shops are investing in sustainable practices. This includes:
- Utilizing biodegradable materials
- Implementing energy-efficient machinery
- Facilitating recycling operations
3. Advanced Materials
The development of new, advanced materials is opening doors for more innovative products. These materials often offer:
- Increased strength and durability
- Lighter weight for reduced shipping costs
- Better thermal and electrical properties
4. Customization and Rapid Prototyping
Companies are increasingly seeking customized solutions. Plastic injection mold shops are responding by offering:
- Rapid prototyping services
- Shorter lead times for custom orders
- In-house design and testing capabilities
Choosing the Right Plastic Injection Mold Shop
Selecting the right plastic injection mold shop is crucial for ensuring product quality and efficiency. Here are some factors to consider:
Experience and Expertise
Look for a shop with a solid track record and experience in your industry. Experienced teams can navigate challenges effectively and provide valuable insights during the design phase.
Technology and Capabilities
Evaluate the technology used in the shop. Advanced equipment tends to yield better results regarding precision and efficiency.
Quality Assurance Processes
Ensure that the shop has robust quality assurance processes in place. Certifications like ISO can be indicative of a shop's commitment to quality.
Customer Support
Effective communication and support are vital for a successful partnership. Choose a shop that actively engages with clients and provides continuous feedback throughout the production process.
Conclusion: The Legacy and Future of Plastic Injection Mold Shops
Plastic injection mold shops are more than just manufacturing facilities; they are the heart of innovation in countless industries. By utilizing advanced processes, sustainable practices, and cutting-edge technology, these shops will continue to play a pivotal role in shaping the future of manufacturing. Companies seeking to harness the power of plastic injection molding must prioritize the selection of a quality mold shop—one that understands their unique needs and can deliver exceptional results consistently.
For businesses looking to thrive in this competitive landscape, partnering with an experienced provider such as DeepMould.net can be the key to success.